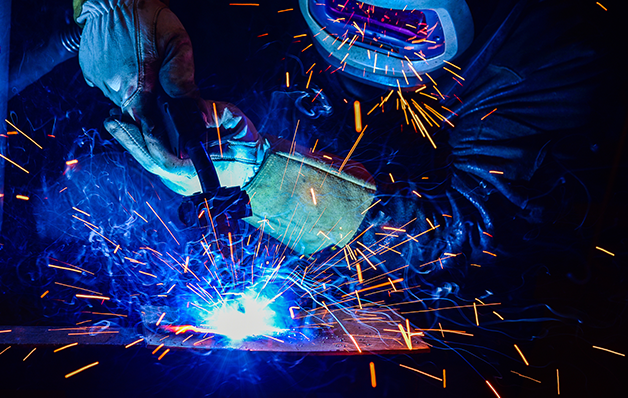
THE PROCESS
MIG (Metal Inert Gas) / MAG (Metal Active Gas), uses an electric arc to fuse materials. In this method, a continuous solid wire electrode is continuously fed through a welding gun, which directs it into the molten weld pool. This technique effectively joins two base materials, creating a strong bond. MIG welding is often favoured for its versatility, speed, and relative ease of use. The shielding gas, typically composed of Argon or a mixture of Argon and Carbon Dioxide (CO2), protects the weld from atmospheric contaminants, preventing oxidation and ensuring a clean weld. Combining the solid wire electrode and the shielding gas makes MIG/MAG welding a popular choice for various applications, from industrial manufacturing to home projects, allowing for precise control and high-quality results in metal joining tasks.
Flux-cored arc welding (FCAW) is a variation of MIG/MAG welding that can be used without an external shielding gas. In this process, flux-cored wire is used, which has a core of flux material that generates shielding gas as it melts during welding. This allows for welding in outdoor or windy conditions where traditional shielding gas might be blown away, making FCAW more versatile in certain environments. However, it can result in more spatter and slag that need to be cleaned up afterwards, and it might not provide as neat a finish as MIG/MAG welding with shielding gas. Despite that, it's popular for its portability, convenience, and ability to weld thicker materials outdoors.
CHOOSING A WIRE & GAS
Wire selection
When selecting your filler wire, it's essential to keep two key factors in mind. First, ensure that the base metal and the filler metal are compatible to achieve a strong and durable weld. The second consideration is the size of the filler wire. Choosing the appropriate diameter is vital for effective welding, as it influences the heat input and the overall quality of the weld.
Gas selection
The choice of gas is influenced by the specific type of metal being welded, as each gas can produce varying effects on the quality of the weld. When it comes to welding aluminum, the requirements shift, and pure argon gas becomes necessary for effective shielding. For mild and stainless steel, the most widely recommended shielding gas is a blend of 75% argon and 25% carbon dioxide.

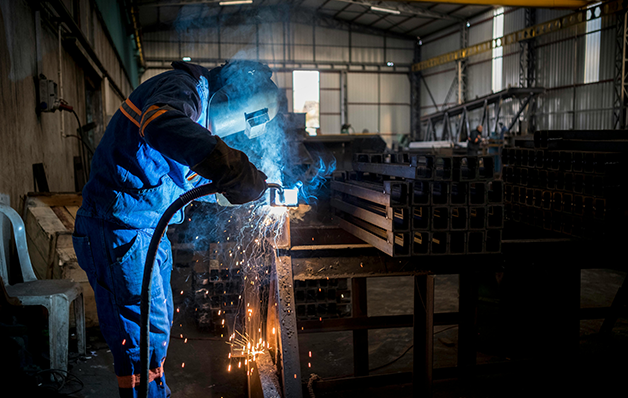
APPLICATIONS
MIG welding is versatile enough to be applied to various metals of differing thicknesses, making it a popular choice in many sectors. Its speed is another significant advantage, allowing for quick and efficient welding processes. These characteristics contribute to its status as the most frequently utilised welding technique in numerous industries.
- Construction
- Automotive repairs
- General fabrication
- Farm repairs
- DIY projects
PRODUCT RANGE
Explore our extensive MIG product range & equipment